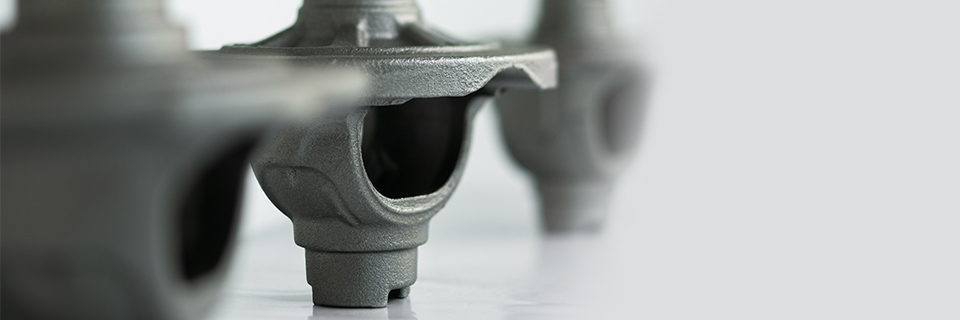
Technical Features当社の特徴トレーサビリティーシステム
高品質な製造ライン
トレーサビリティシステムにより高い品質の製造ラインを構築しています。
従来の不良対策は過去の経験と勘に頼るモグラたたきと呼ぶ取り組みであり、対策直後は不良が減るが真の対策が出来ていないため、時間が経つと不良が再発するのが普通でした。
しかし、当社ではトレーサビリティシステムを導入しています。このシステムによりトリベ単位で製造条件がトレースでき、尚且つ、自動計測により取れる限りの製造条件データを計測できるため、全てデジタル化して記録することで市場からのクレームリスクを最小限にすると同時に、そのデータを解析することで、不良の真の原因を解明し、確実に不良が低減出来る工程を構築しています。
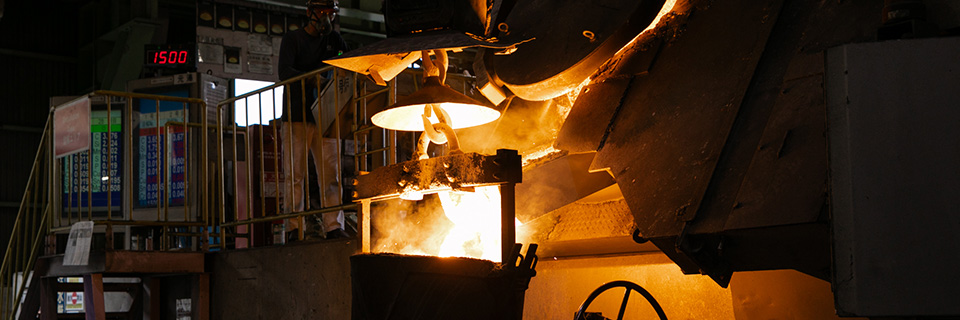
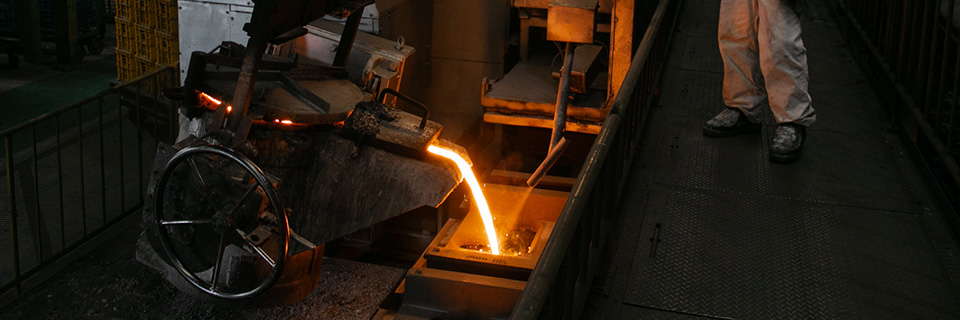
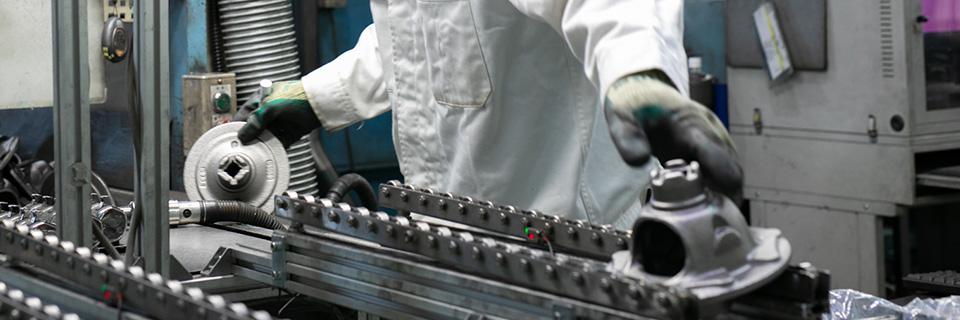
高い品質を実現する
当社の取り組み
以下の取り組みを行うことで高品質な製品を製造し、お客様から高評価をいただいています。
1個単位で追跡できる
トリベ単位から1個単位の管理へ
マーキングロボット開発の成功により、従来のトリベ単位の管理から、1個単位での製造条件のトレースが可能になりました。その結果、お客様には「トレーサビリティを確保した製品」をご提供することが可能となり、当社とお客様のクレーム発生時のリスクを最小化することが出来ます。
製造条件をノウハウとして蓄積することで得た高品質[オーダーメイド]
自動計測によるデジタルデータの見える化
デジタルデータを見える化することにより、作業員はブラックボックスであった自分の仕事の結果をその場ですぐに確認することが可能になり、技能・モラルの向上につながっています。
また、ご見学いただいたお客様に当社の品質に対する安心感を持っていただいております。
徹底したシステム教育が従業員の意識向上につながり従業員のレベルアップへ
従業員のトレーサビリティーマインドの定着化
「不良ゼロ」にチャレンジできる強力なツールを持つことで全社的にトレーサビリティーマインドが定着してきております。自動計測しているデジタルデータだけでなく、3現主義による現場での気付きも有効であるため、デジタルにアナログ的考えを取り入れたデジアナ改善も行っております。
トレーサビリティの効果
トレーサビリティシステムの概要
改善1球状化処理/溶湯重量自動計測・デジタル化
改善前バネ式クレーンスケール
- 問題点
-
- 正確に計量するのが難しい
- 受けた量が記録に残らない
改善後無線式デジタルクレーンスケール
デジタルクレーンスケールを設置することにより、デジタル画面が読み取りやすくなり作業性が向上、デジタルデータを転送できるようになり、計画と実績データが記録に残るようになりました。
改善2球状化処理剤の自動軽量・デジタル化
改善前Mg手動計量
- 問題点
-
- Mg手動計量
- 計量記録が残らない
改善後Mg自動計量
Mg自動供給装置へ変えることにより、計量を自動化し、またデジタルデータを転送できるようになり、実績データが記録に残るようになりました。
改善3フェーディング時間(球状化処理~注湯完了)の自動計測、デジタル化
改善前
- 問題点
-
- フェーディング残り時間が分からない
- フェーディング時間の記録が残らない
改善後カウントダウンタイマー設置
カウントダウンタイマーを設置することにより、フェーディング(残り時間)を表示させ作業性を向上、またデジタルデータ転送できるようになり、残り時間が記録にも残るようになりました。
改善4非接触 注湯温度自動計測システム
温度測定方法
- 赤外線放射温度計(非接触)
注湯回数:20~30枠/トリベで従来の熱電対浸漬方式では全鋳枠の注湯温度測定は非効率
- 測定ポイント「注湯トリベ鳥口」
-
- 新生面でノロ、酸化スケールの影響小
- 溶湯表面の凹凸小→熱放射安定
- 回りに壁がなく、壁から幅放射なし
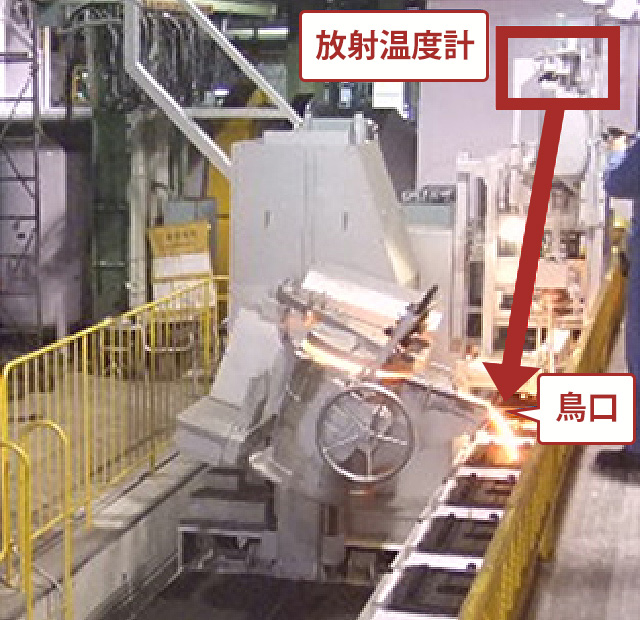
活用事例
トレーサビリティ・システムを活用した改善事例を一部ご紹介します。
活用事例1ごみかみ不良対策
分析
トレーサビリティーデータより、
- 特定の作業者が中子入れをした時に多く発生している
- 鋳込み速度が社内平均よりも20%以上速い
ことが判った。
対策後
改善前に比べて改善後は、ごみかみ不良率が「50%減少」しました。
活用事例2湯回り不良対策
分析
トレーサビリティーデータより発生傾向に連続性があることが判明、
- 注湯温度が一定温度以下の時
- ライン停止直後
に集中していることが判った。
対策後
改善前に比べて改善後は、湯回り不良率が「95%減少」しました。